Project Name: EnergySeal Headquarters Architect: VY Architecture Project Completion: August 2019 Project Location: 14037 HWY55, McCall, ID 83638 Project Type: Energy Efficiency Commercial
Project Description
EnergySeal Headquarters, located in McCall, Idaho, is a 16,000-sf office and warehouse building designed and built for a high-performance insulation contractor. The goal of the project was to create a modern, ultra-energy-efficient building in the harsh climate of Idaho’s central mountains, where winters can exceed 10,000 heating degrees days (more than Moscow, Russia). Heating such a large space in a cold climate is costly, so to reduce long-term operating costs, the facility employs an extremely well-insulated envelope to reduce heating loads.
The entire building (11,000 square feet of warehouse and 5,000 square feet of office space) will be certified to meet the PHIUS+ Passive House standard. In addition, the office space is designed to be Net-Zero with renewable energy generated onsite by a façade-mounted PV array.
EnergySeal Headquarters is among the most energy-efficient building in North America, with a measured energy use intensity (EUI) after the first year of occupancy of 14.85 kBTU/sf/yr before renewable energy production.
After the electricity generated by the 14.7 kW solar PV array is accounted for, the EUI becomes 12.0 kBTU/sf/yr, which allows the building to meet the 2030 Challenge 80% reduction from the baseline site EUI target.
By committing to an aggressive energy target early in the planning stages, even a challenging project type such as a warehouse can result in an ultra-low energy building capable of cost-effectively reaching net-zero without overly complex and expensive mechanical renewable energy systems.
Type of construction materials, mechanical systems, and any other pertinent technical information
The project team achieved aggressive levels of energy efficiency by focusing on designing and executing a high-performance building enclosure that relies on super-insulation, high levels of air-tightness, and thermal bridge-free design.
The building was modeled using the WUFI Passive energy-modeling software to optimize the building enclosure, mechanical systems, lighting, and PV system. This detailed modeling assured that the annual heating and cooling demands and overall source energy usage would meet the stringent PHIUS+ certification standards.
All structural components were carefully modeled and designed to ensure that thermal bridging was minimized and accounted for in the energy modeling.
The high-performance wall and roof systems utilized a combination of HFO low-global warming potential (GWP) spray foam and ultra-low embodied energy plant-based cellulose insulation composed of 85% paper fiber.
The high-performance R-8 windows utilize R-11 triple-pane glass with low conductivity frames. Motorized external Venetian window blinds control solar gain and glare to minimize the cooling load and maximize indoor environmental quality for occupants year-round.
The ultra-efficient building enclosure allowed the building to be heated with a very simple HVAC system. A single 4-ton variable capacity cold-climate air source heat pump serves the entire warehouse space. The office portion of the building is served by a 3-ton heat pump with an integrated intelligent communication system that provides zone control through modulated dampers and smart controllers. The office space is ventilated using an 87% efficient heat recovery ventilator (HRV), controlled by an indoor environmental sensor that modulates the ventilation rate based on real time occupancy and indoor air quality.
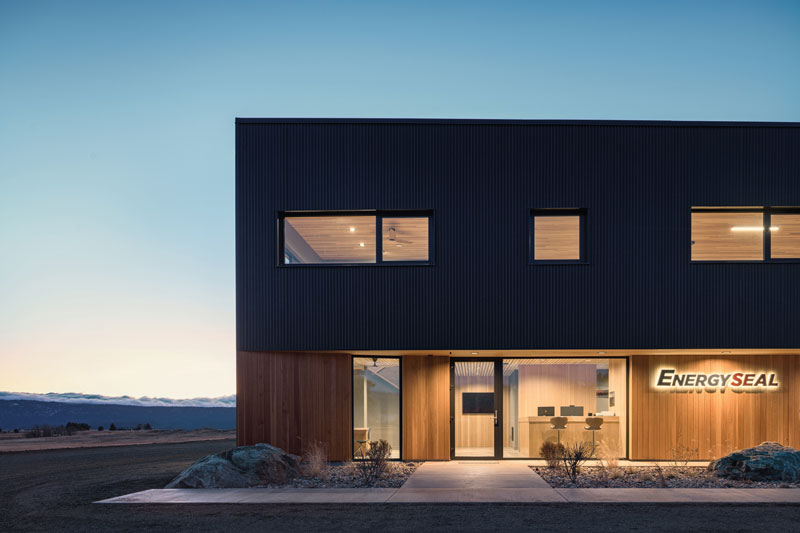
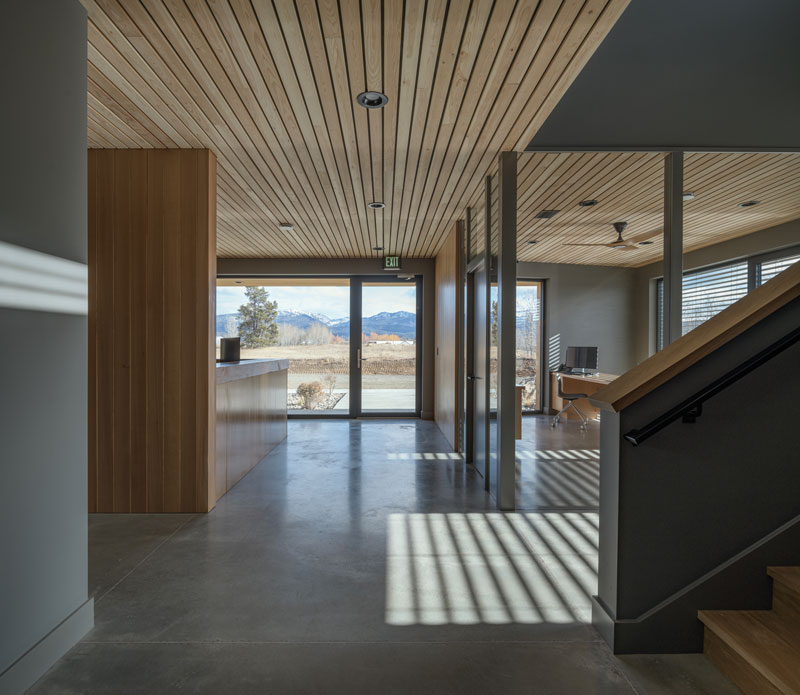
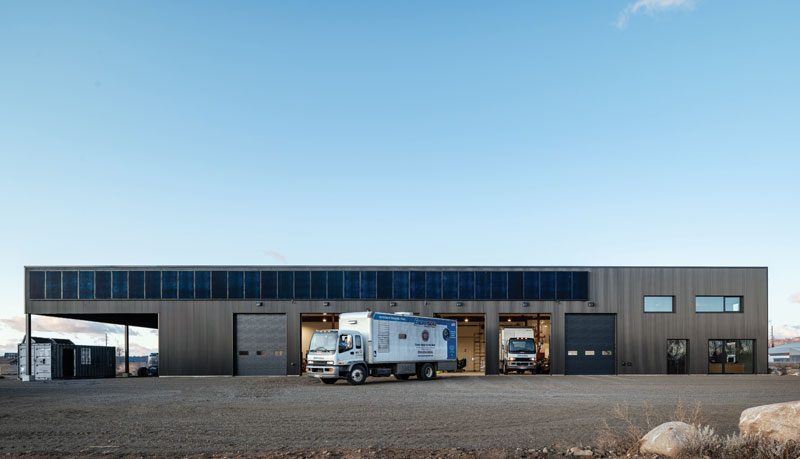
