Some insulations do a better job at paying back than others.3
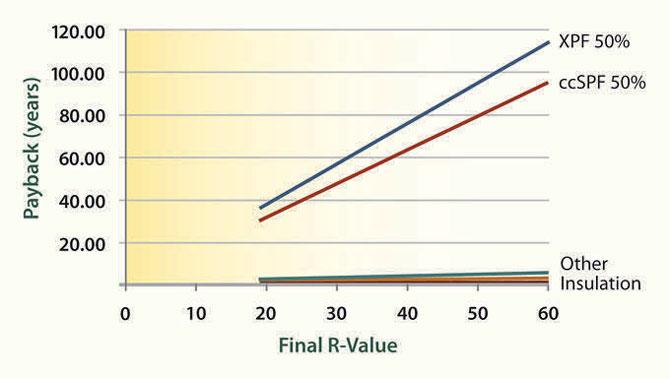
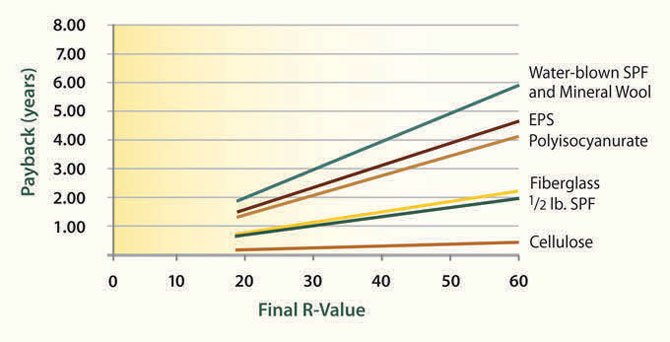
Next, we should examine which components of the building are significant enough to impact the overall embodied carbon: structure, insulation, and HVAC systems are the big ones. There’s a lot of “stuff” in the structure and insulation of a building, and these are the main aspects to target first. HVAC systems have much less “stuff,” so it is not intuitive to think that these components have a significant impact. Refrigerants in heat pumps and air-conditioning systems are the culprit, and a simple refrigerant leak can wipe out any measures taken to reduce the operational or embodied carbon of a good building. We’ll focus on the assemblies, or the “stuff” in this article, but there is also a good reference read about refrigerants4.
1. Cheaper is better.
Say what?! Not always, but Occam’s Razor holds true in many instances of construction as well as in physics (because building is physics!). The simplest, least-expensive solution is often the best for the planet.
There’s so much to unwind in this subject, but in general, less processed and especially plant or bio-based materials have low-carbon impacts. In the case of plant-based, there is potential for carbon storage, depending upon the practices of the harvesting and processing, i.e., forestry or farming practices, lumber company, the mill, transportation, etc.
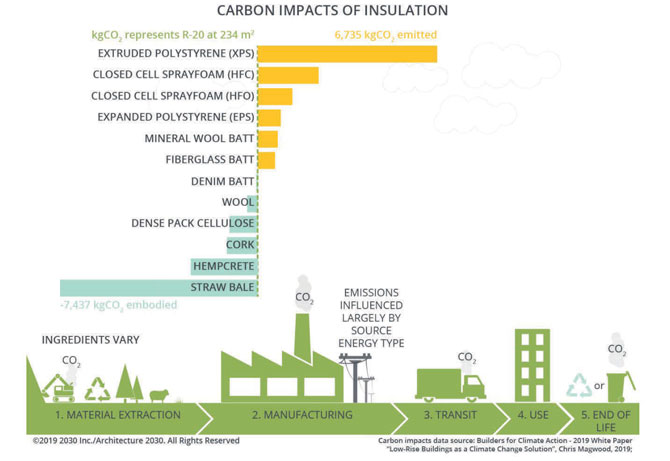
A good rule of thumb is to use wood instead of steel or metal framing as much as possible and use plant-based insulation whenever possible. If you can specify FSC or SFI wood products, then you will have a carbon storage effect. If not, at least the number will be low.
Although wood is not as sleek or low-profile as steel, a great side benefit of wood is that it has far less thermal conductance and therefore helps to reduce thermal bridging and condensation within assemblies, which helps a building stand up longer. (Cross-laminated-timber [CLT]) is beautiful and regional and can replace steel or concrete in many instances. CLT is produced regionally by SmartLam [smartlam.com].)
If you cannot use cellulose, hempcrete or straw, then use fiberglass, hemp batts (not shown on the graph, but fall between denim and wool, which will very soon be Idaho-produced; see hempitecture.com), or anything besides XPS and spray foam.
The second aspect of “cheaper is better” is that a code-built (yes, even an Idaho code-built building with R-values from 2009) can actually be better than a high-performance building.
Anything with super high R-values that is relatively thin (XPS, spray foam) took a considerable amount of energy to produce. We love Passive Houses, but when packed full of high-energy foam insulation (spray foam or XPS), they probably have done more harm than good, and their payback period may be more extended than the functional life of the building. And at any rate, it is much longer than we have time to curb climate change. A Passive House insulated with cellulose, on the other hand, will do good by the climate over a relatively short period of time. And the payback period is short.
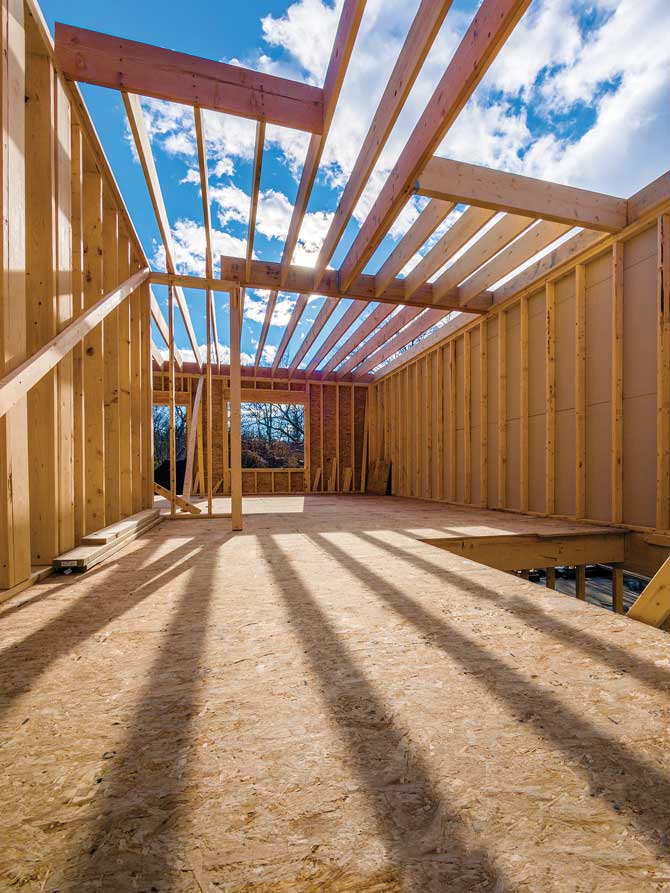
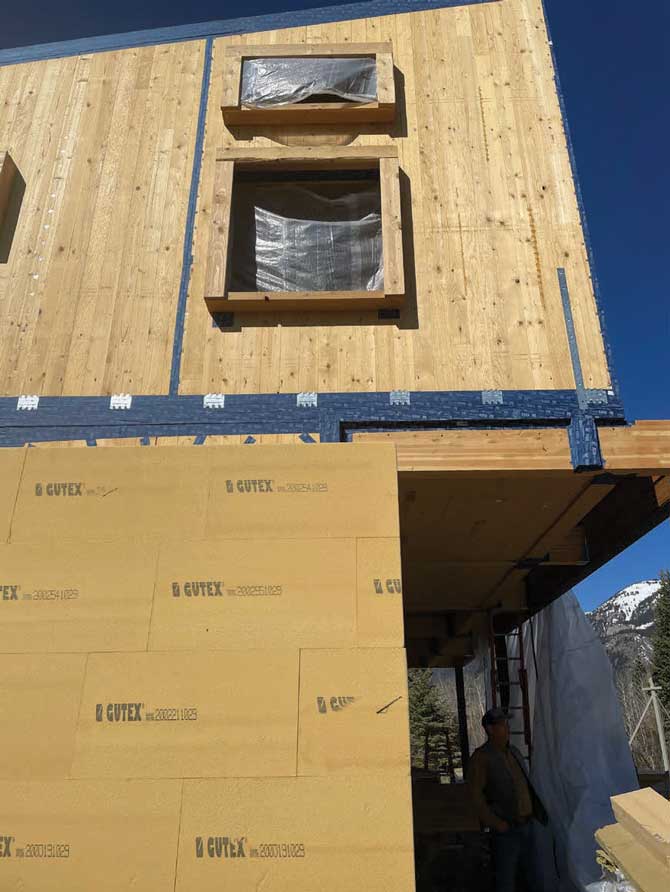
Credits: Love | Schack Architecture – CLT structure w/ Gutex insulation
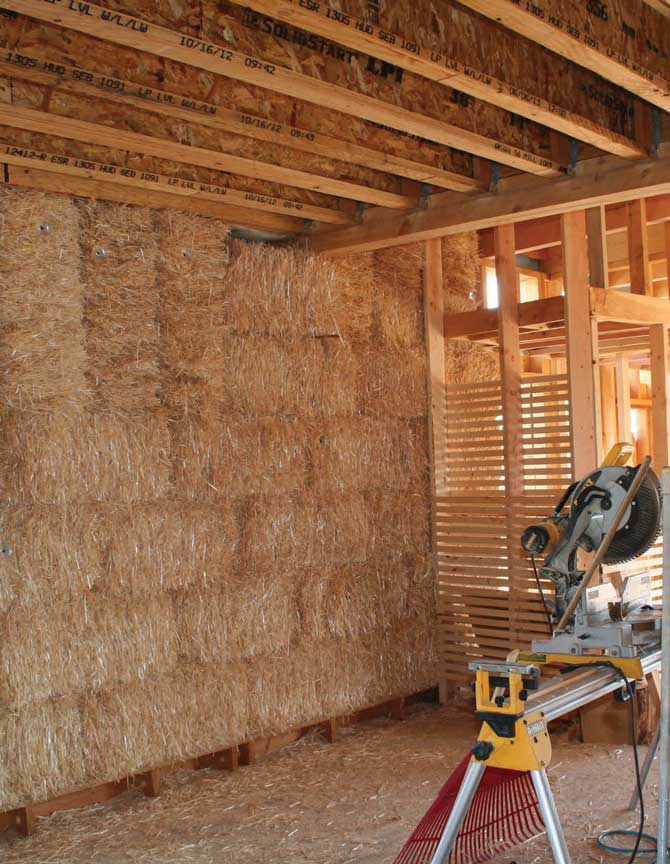
Credits: Love | Schack Architecture –
strawbale insulation
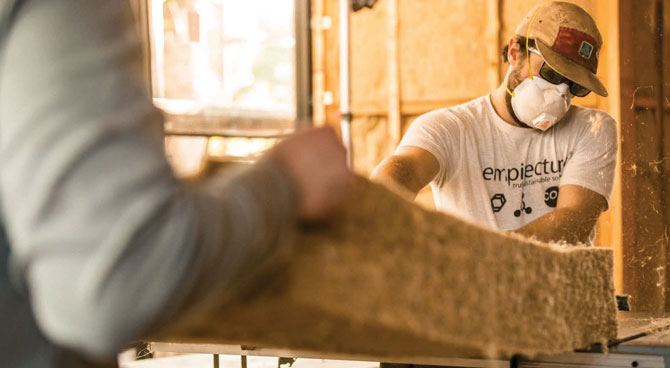
Credit: Hempitecture – hemp batt insulation
2. So you’ve chosen to use low-carbon materials – great!
Now you have to ensure the flat roof is air-tight to keep your roof sheathing from rotting, how to get a good R-value in the walls, and what to use below grade. Implementing these materials in an already reasonably designed building may not be possible without making significant changes, but it might.
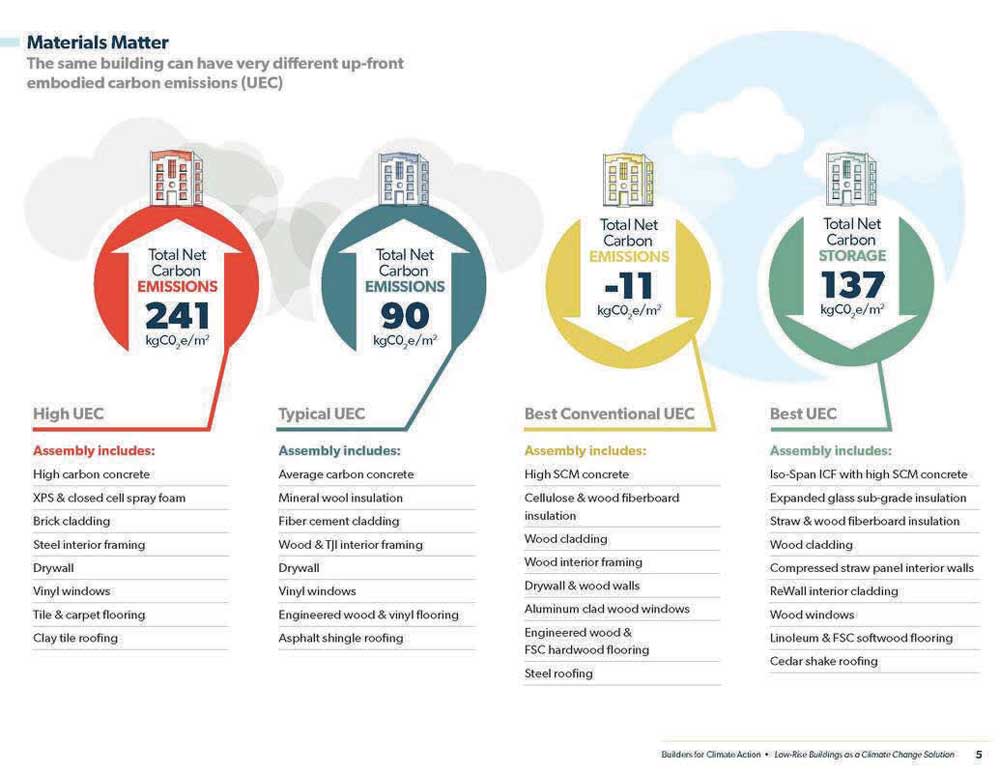
From the top down, here are some guidelines:
Roofs: again, cheaper is better: Whenever the design allows for a simple wood truss-roof with blown-in insulation and venting above the insulation, do this! And allow for a good, high-energy heel. Good design can work around aesthetic challenges. Embrace the energy heel and work with it. Every contractor knows and loves this system. Implementations challenges will be low.
When the design calls for a low-slope, flat, or vaulted roof, you have more limited options, but there are still options. The most conventional strategies are to “flash-and-batt” or add rigid insulation over the sheathing. Minimize the amount of rigid or foam insulation you use, but it must be adequate enough to prevent condensation. As always, use mineral wool (Toprock) or EPS, or anything besides XPS. Maximize the amount of dense-packed insulation. You can get air-sealing with the flash and batt strategy, but only as long as the spray foam does not become brittle and crack, and only if installed correctly. In the high-performance building science community, spray foam is not considered a “durable air seal.” But, based on the availability of innovative, educated, or like-minded contractors, this may be the option with the least harm.
The next option, when adequate slope allows excellent venting, a structural rafter, truss, or joist roof dense-packed with low carbon insulation can be covered with a cold roof such as this5.
In areas where labor is extremely expensive and depending upon the pitch of the roof, contractors may argue that this is more expensive than spray foam. It is possibly true, but it is not necessarily true. It depends on the contractor more than the system.
For a flat or low-slope roof, it is more imperative that the contractor be educated and willing6. A high-R-value, dense-packed roof such as the one above can be left unvented if there is no chance of moisture entering the insulation cavity and if whatever moisture may sneak its way in can get out. This requires excellent air sealing with tapes and caulks at every penetration and a chase to eliminate most penetrations, such as an electrical chase framed below the roof framing. This assembly is risky, and building scientists argue about how risky. Idaho has, in general, a very dry climate, so the risk is lower here.
In the two dense-packed options, the use of “smart membranes” and excellent air sealing is crucial. A smart membrane with smart installation and a plan for applying it at each junction keeps moisture vapor out of the assembly and allows it to escape to the interior. Not every contractor is aware of smart membranes, but there are some common options, and most contractors in our market are familiar with CertainTeed products and will be more open to this version, Membrain, rather than an unknown brand. Performance, installation, and permeability vary, but an article discusses the most common7.
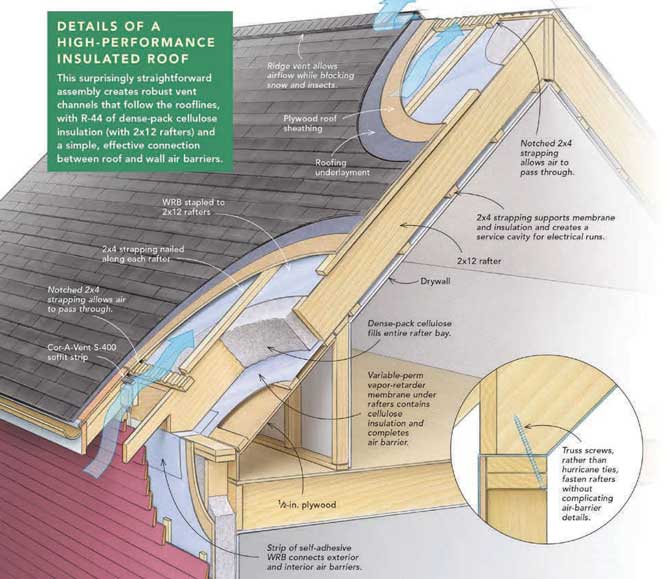
Credit: FineHomebuilding
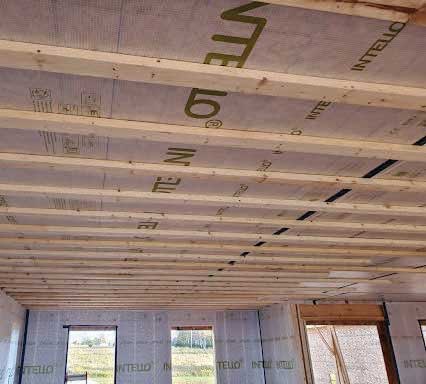
Credit: 475 Building Supply
- Exterior insulation provides better performance by reducing thermal bridges, and we benefit from keeping the sheathing warm, thus avoiding condensation. It creates some challenges with fastening siding, but this is a reasonably conventional practice nowadays, and most contractors have gotten over their fear that the fastening will fail. We know that the compression of the fasteners can provide enough friction to overcome the force of gravity. Different insulations have some performance aspects to consider, such as how water, air, and vapor interact. This is important to learn because the WRB must be installed differently with, say, mineral wool boards than with wood fiberboard.It is possible that rigid wood fiberboard could be the game-changer in reducing embodied carbon in buildings. Some of the products can act as the WRB, thereby reducing labor costs, and some provide shear support – thereby eliminating the need for sheathing in some seismic zones8. The only current producers are in Canada and Europe, but GoLab will come online in Maine in the near future9.
- Interior insulation can be increased by widening the framing, either by using 2×8 instead of 2×6 structural walls or adding an extra wythe of minimal 2×3 or 2×4 framing. Often spray-foam loyal contractors will agree that the extra cost of 2×8 framing lumber will offset the cost the stem wall because of wicking.
- EPS, mineral wool, and foam glass (not on the chart of insulations) are three relatively easy options for of foam insulation, so they can’t argue that “thicker walls are more expensive.” The R-value of a 2×8 wall with cellulose or batts is still not quite as high as the R-value of a 2×6 wall with spray foam. Still, most contractors will advocate for flash and batt over filling the entire cavity with foam, so even if they build a 2×8 wall but ultimately go with their preference of flash and batt, the harm of foam is still reduced. If they end up filling the 2×8 cavity, well, then, you did more harm, but you also will have learned a lesson (personal experience) – work with contractors you trust and clients who trust you.A double-stud wall is a can of worms in terms of options for thickness and insulation options. It’s less conventional and more challenging to frame. But because of the options it can be the right choice if you have a client who is willing to push the sustainability envelope with an alternative insulation such as straw bales10.
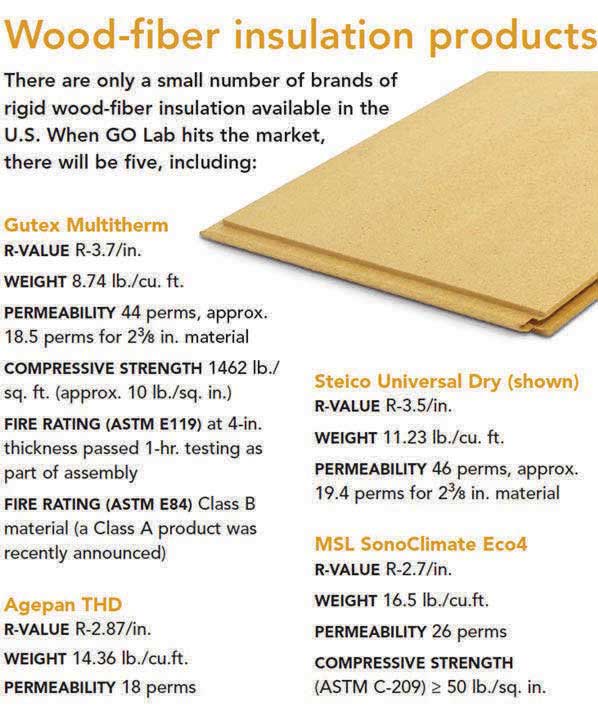
Credit: FineHomebuilding
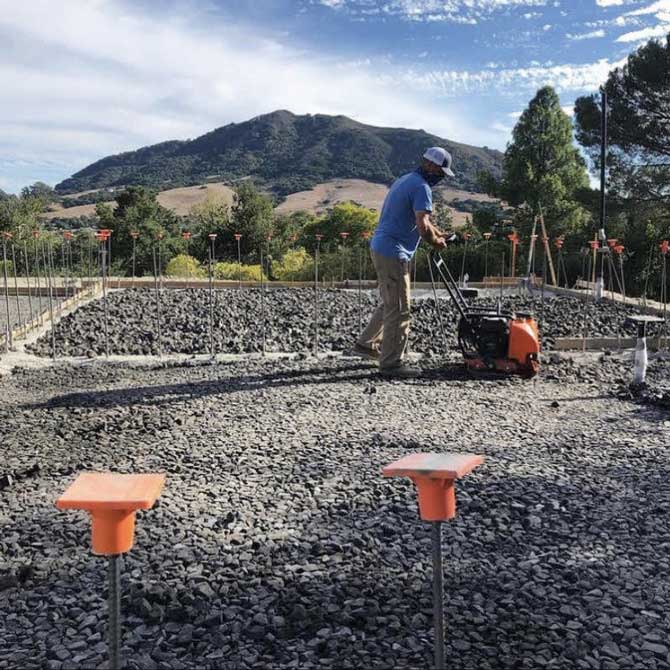
PC: Cairn Collaborative
Panelization helps us to conventionalize and control the worms in the can. When we start talking panels with contractors and clients, people care less about what is inside the panel and more about how much time they can save in a short building season. This can be a great strategy for bringing everyone over to your side. There is risk with panelization and there is more upfront investment. The panel company must be reputable and the shipping should not overwhelm the savings. Some reputable American and Canadian panel companies include:
- Tectoniks: bensonwood.com/tektoniks
- Collective Carpentry: collectivecarpentry.com
- Ecocore: ecocor.us/enclosure-systems-2
- New Frameworks Gryphon Panels: Ecococon https://ecococon.eu are excellent European panel companies looking for U.S. projects so they can begin to manufacture in the states.
Foundations are challenging. Water and biodegradable materials do not mix and this is the most vulnerable part of the building. It is hard to get around using a higher-energy insulation while also preventing mold and rot. You must first decide if the insulation should be interior or exterior and to how much moisture it will be exposed.
Exterior: If it is porous and the ground is wet, then the insulation value will disappear.
Interior: A conditioned crawl space can help to control the humidity, but insulation must be installed properly against this part of a building. Mineral wool is porous, but more conventional and be both in and outside of a stem wall. EPS has higher carbon footprint, but can be under a slab (specify compressive strength) or on a wall, inside or out. Foam glass is not yet conventional but replaces gravel.11
Interior: A conditioned crawl space can help to control the humidity, but insulation must be installed properly against this part of a building. Mineral wool is porous, but more conventional and be both in and outside of a stem wall. EPS has higher carbon footprint, but can be under a slab (specify compressive strength) or on a wall, inside or out. Foam glass is not yet conventional but replaces gravel.11
3. Work with contractors you trust and clients who trust you (the second part comes easily when you start with the first part).
This can go either chicken or egg first, but if you are adamant that your clients will be better served by working with a contractor on your team, then you will all more easily achieve the clients’ goals. This works very well, most of the time. If you do not have a contractor you trust in your circle, then reach out to different certification programs to find out who in your region is educated and interested. The construction industry is not as savvy about embodied carbon as they are about energy efficiency, in general, but EMU provides affordable contractor training for Passive House methods that is very well done. Though they do not focus on embodied energy, they educate with various types of materials and methods, so contractors are exposed to all the options.
4. Take the easy way out, reduce friction.
We must circumvent the “spray-foam as a do-it-all in one strategy.” Embrace membranes, tapes, and caulks, and then support your contractor through the “how to” – reduce the friction they feel about learning a new system. Take time to think through sequencing of installation of framing and membrane components and get their input. A little planning goes a long way toward reducing labor on site. Once you do it will be second-nature, just like spray foam is currently for many. Also: avoid gable trusses! They are really challenging to air-seal with membranes and tapes.
5. Take responsibility.
Your client hired your company for many reasons and they do not need to know how all the sausage gets made. They probably don’t care about the sausage as much as you think they do, so just do what you do.
6. Forget about embodied carbon (when talking with contractors and especially clients).
Most people don’t get it yet. Someday this will be mainstream terminology, but until then, our job is far easier when we speak the same language as clients. Communicating about a healthy indoor environment is something that everyone will be on board with from the beginning. It just happens that many high carbon materials also contribute large loads of toxins to our environment and potentially indoor air. Healthy materials is a parallel route leading to the same destination (unless we’re talking about manufactured antimicrobials, but that’s another story).
7. Just do less harm:
if everyone would start building high performance straw and hemp commercial and institutional buildings and singing Kumbaya tomorrow, that would be amazing. In the meantime, use your intuition to evaluate what you can bite off now and do it without looking back. Use each failure to learn and improve.
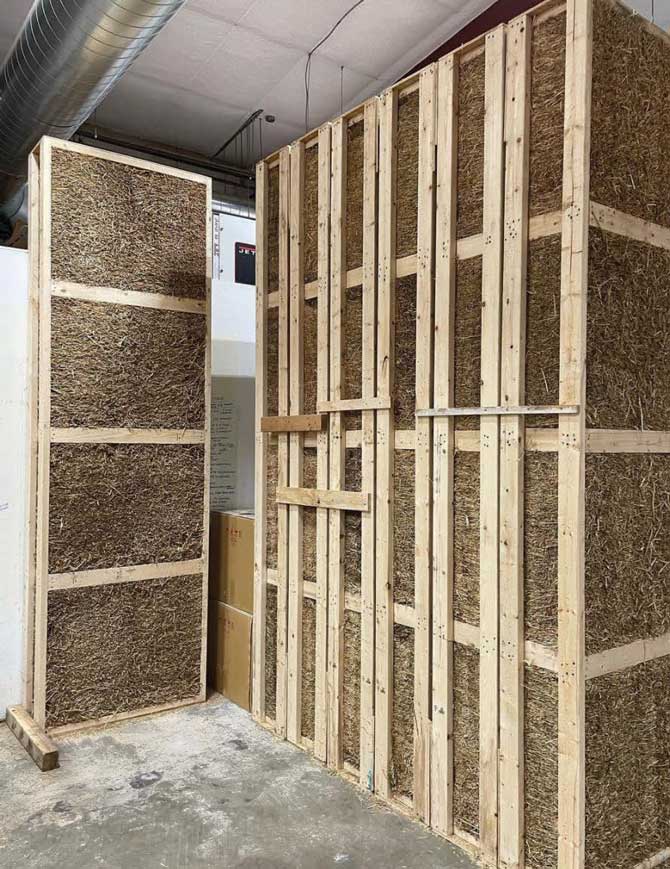
Credit: New Frameworks
1 https://blueprintforbetter.org/articles/design-resources-to-help-stop-climate-change/
2 https://www.buildersforclimateaction.org/whitepaper1.html
3 https://www.buildinggreen.com/news-article/avoiding-global-warming-impact-insulation
4 https://www.greenbuildingadvisor.com/article/reducing-refrigerant-leaks-from-heat-pumps
5 https://www.finehomebuilding.com/2021/04/28/a-new-take-on-insulating-a-roof
6 https://foursevenfive.com/blog/the-ten-golden-rules-for-foam-free-flat-roofs/
7 https://www.finehomebuilding.com/project-guides/insulation/smart-vapor-retarders-for-walls-and-roofs
8 https://www.finehomebuilding.com/project-guides/insulation/284-in-favor-of-wood-fiber-insulation
9 https://www.timberhp.com/
10 https://www.greenbuildingadvisor.com/article/a-case-for-double-stud-walls
11 https://www.owenscorning.com/en-us/insulation/foamglas?adobe_mc=MCMID%3D90569524272236196302559584395362591500%7CMCORGID%3D3AED27E253DB1E4C0A490D4E%2540AdobeOrg%7CTS%3D1638747205;
https://www.glavel.com/foam-glass-gravel/